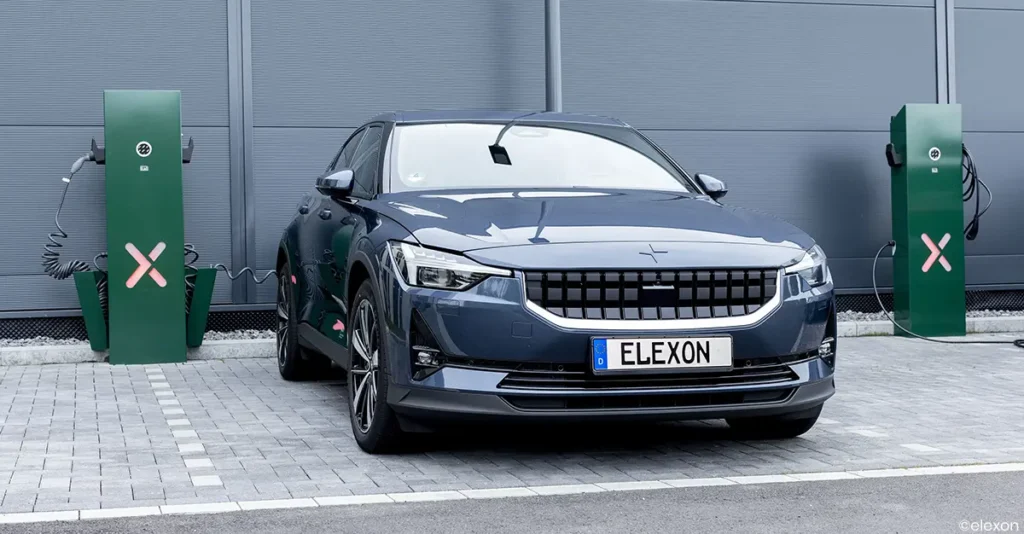
Blending electrification trends and sustainability goals with digital solutions
The market for electric vehicles has grown significantly. As a 360° system integrator, elexon uses
Opportunities to progress/be leaders |
16,1%
|
Flexibility, i.e., remote working, flexible hours |
13,4%
|
Sense of meaning from my work |
9,3%
|
Professional development training |
8,3%
|
The impact it has on society |
6,8%
|
The quality of its products/services |
6,4%
|
Strong sense of purpose |
6,2%
|
Opportunities for international travel |
5,9%
|
Fast growing/dynamic |
4,4%
|
A company that values its employees |
4,3%
|
Use of the latest technologies |
4,1%
|
Reputation of the managers |
3,1%
|
The market for electric vehicles has grown significantly. As a 360° system integrator, elexon uses
TÜV SÜD Energietechnik digitizes its processes with the smart service platform from oculavis. New standards
Holcim, a leader in the construction industry with 63,000 employees worldwide, has recently integrated the
In a remarkable achievement that underscores the transformative power of digital innovation in customer service
Networking, automation, and data-driven services provide valuable insights into production processes in mechanical and plant
As a successful provider of visual assistance and augmented reality solutions, we can state one
The market for electric vehicles has grown significantly. As a 360° system integrator, elexon uses
TÜV SÜD Energietechnik digitizes its processes with the smart service platform from oculavis. New standards
Holcim, a leader in the construction industry with 63,000 employees worldwide, has recently integrated the
In a remarkable achievement that underscores the transformative power of digital innovation in customer service
Networking, automation, and data-driven services provide valuable insights into production processes in mechanical and plant
As a successful provider of visual assistance and augmented reality solutions, we can state one
KraussMaffei and oculavis introduce a service platform for maintenance and service in the VDMA magazine
Open exchange sessions between the participants of the ARxelerator program currently take place every Friday.
In September 2021, oculavis GmbH and ISAP AG celebrate their second partnership anniversary.
As the leading full-service provider for the cement industry, the cement technologies business unit of
SCHNAITHMANN is a system integrator and automation specialist. With 245 employees
The current situation has changed a lot: We are shopping with mouth-and-nose masks, have reduced
Tier 1 automotive supplier thyssenkrupp Bilstein relies on oculavis SHARE to connect its production sites
The GEBHARDT Intralogistics Group has successfully established a digital business model in after sales service
In the course of the Corona Pandemic, a large number of industrial companies have completely
PRODUCT
Smart Service & Connected Worker Platform
Ticketing & Work Order Management
Standard Operating Procedures
Visual Assistance
Service Access Point
Management & Configuration
Integration
White Label Solutions
Secure & Scalable in the Cloud
Pricing & Licenses
SOLUTIONS
Machinery & Equipment Manufacturing
Manufacturing Industry & Automotive
Energy & Utilities
Pharma & Life Sciences
Construction Machinery & Off Highway
Certification & Industrial Services
Customer Service
Technical Field Service
Acceptances, Inspections & Audits
Technical Sales & Consulting
RESOURCES